Greensand molds with gating system.
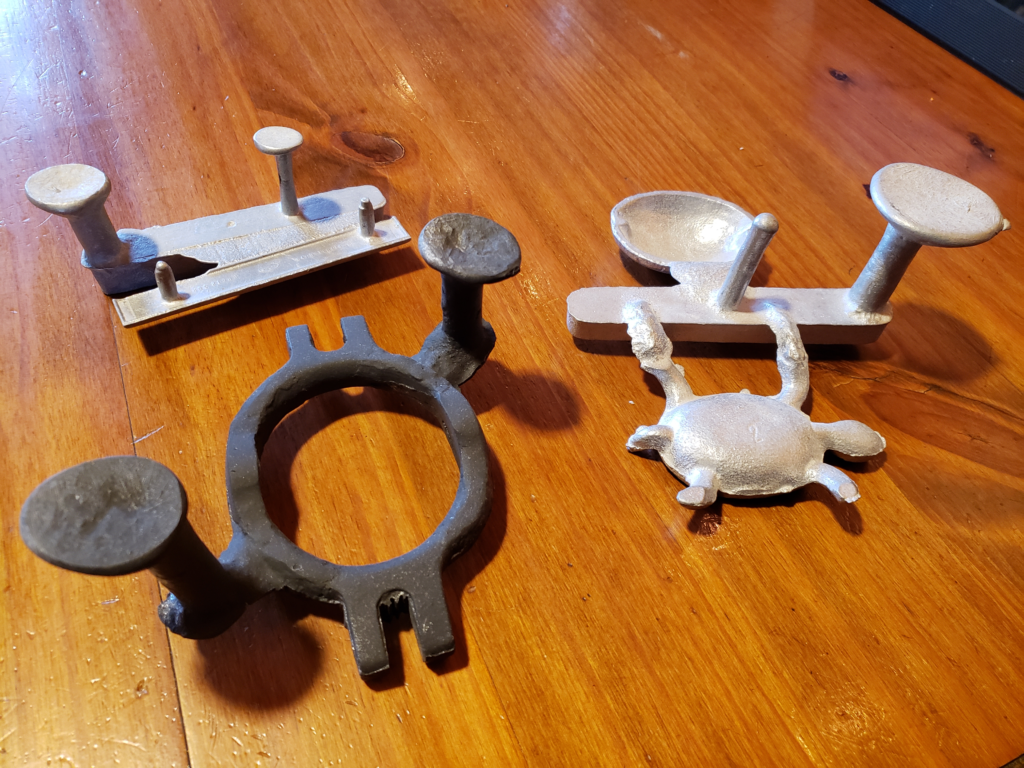
Gating iron (Latin: ferrous) is different than gating aluminum or bronze (non-ferrous). Dross is produced with non-ferrous alloys , but NOT with iron. Dross is similar to the foam on top of beer.
When gating non-ferrous castings, dross is carried beyond the gate by the deep runner, clean metal enters the casting.
When gating iron, the metal is so heavy, 2 large openings (sprue/riser) are used to equalize the pressure.
Parameters of Gating
Alum castings 3lbs. or less- Bronze castings 9lbs or less
1/2″ sprue, 1″x 1″ runner up to 10″ long.
Alum castings 3-8 lbs.- Bronze 9-24 lbs.
3/4″ sprue, 1.5″x 1.5″ runner up to 14″ long.
Alum castings over 8 lbs. Bronze over 24 lbs.
1″ sprue, 2″x 2″ runner up to 18″ long.
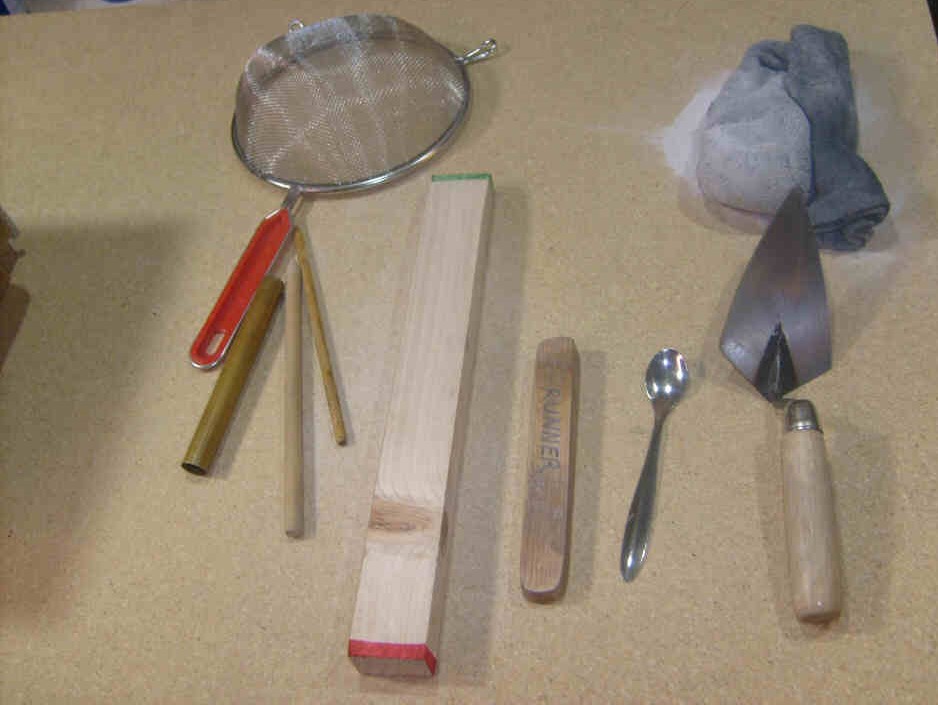
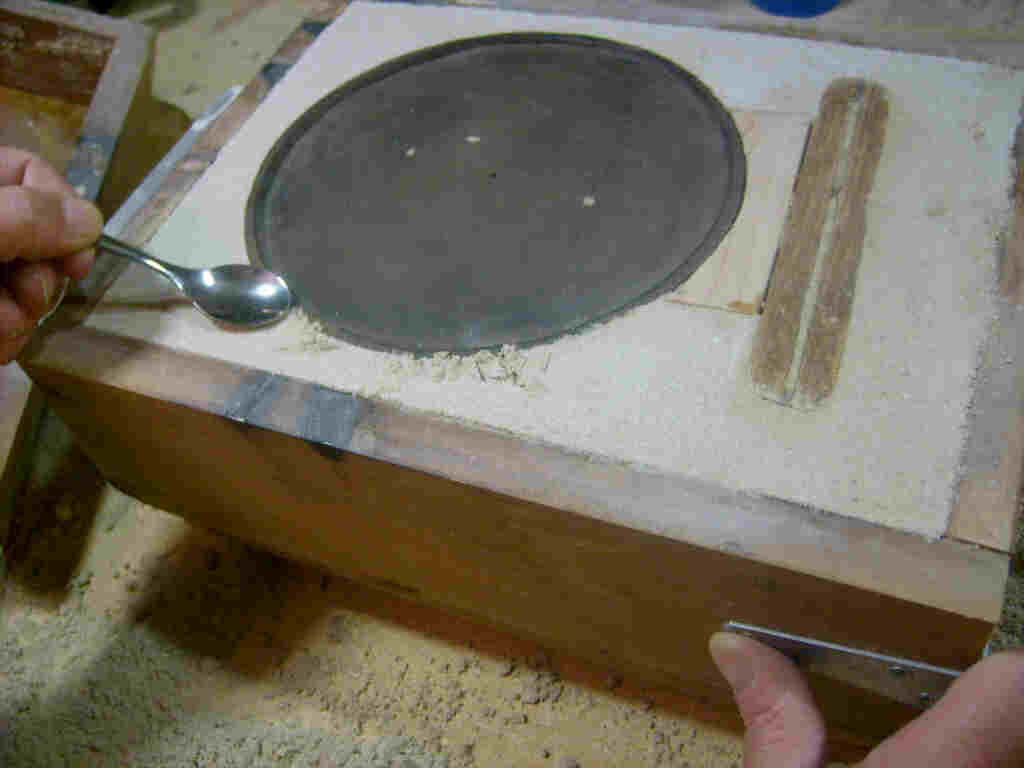
and carefully removing the pattern.
The most important molding tool is your finger. Push to smooth rough areas when molding, do NOT rub, push (press).
Molding flasks
A flask has 3 parts. Drag (bottom), cope (top) and a board in between. The pattern board, place loose patterns here when ramming the drag. Patterns permanently attached to the pattern board is called a matchplate.
Molding Steps:
1. place pattern/runner in the drag section of the flask, the side with pins. About 1/2″ or more from the edge of the flask. Place sand in the flask loosely and ram gently with each stroke about 1″ apart, ram again more firmly. Fill flask about 2″ past the top, ram it down flush with the flask.
2. Strike off drag with a straight edge. Add a handful of loose sand to the flat surface. Place a bottom board on the drag and flip the whole mold. Clamp if it weighs over 100 lbs.
3.Remove cope and pattern board. If your pattern has an odd shape or is round you must cut down to the parting line, the equator on a globe. Smooth all areas you cut with a molding spoon. Replace cope section and apply parting dust. Parting is “hydrophobic”, it repels moisture. Most powders absorb moisture and are not suitable for parting.
4.Fill cope section with loose sand, ram gently with strokes about 1′ apart. Ram sand again a little harder. Fill again, very full, about 2″ over the top. Ram with strokes about 1″ apart until flush with the top. Strike sand level with a straight edge and smooth with a trowel.
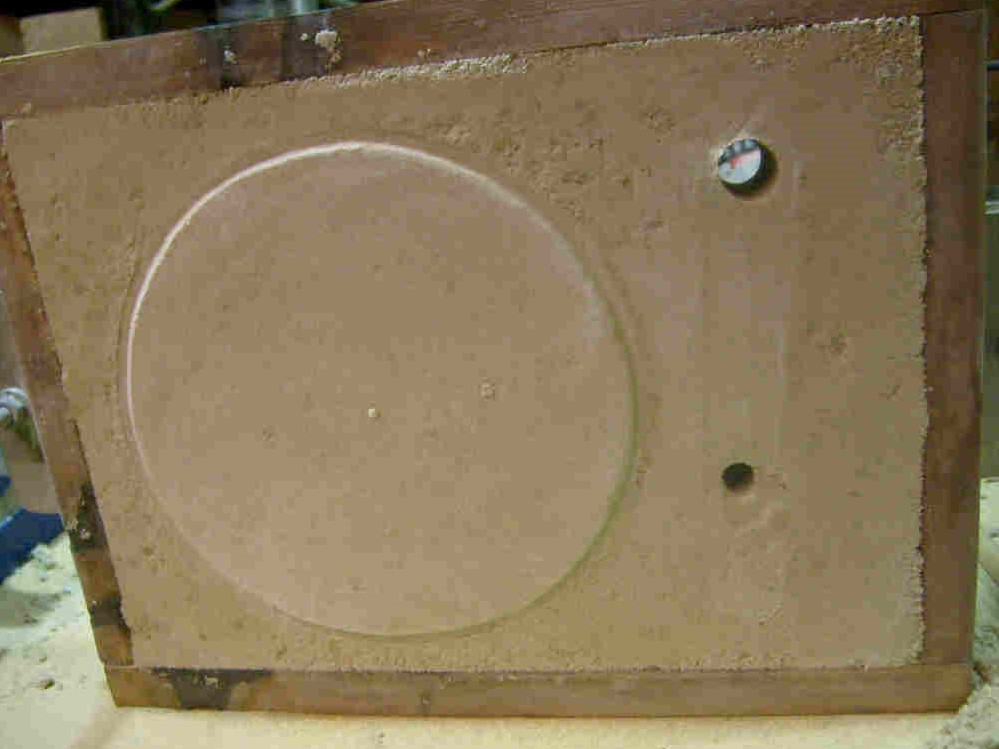
6. Drag section. Tap runner pattern to loosen and remove. Cut gate from runner to pattern, slightly less thick than the pattern. Smooth everything you cut in the sand, erosion will carry loose sand into the casting. Tap pattern to loosen from sand, this step is very important. Remove pattern with surgical skill.
7. Replace cope onto the drag. Clamp or weight up the mold if you are pouring bronze, brass or cast iron. Clamp aluminum molds if casting is more than 70% of the surface area of the mold. Move mold to pouring area and pour.
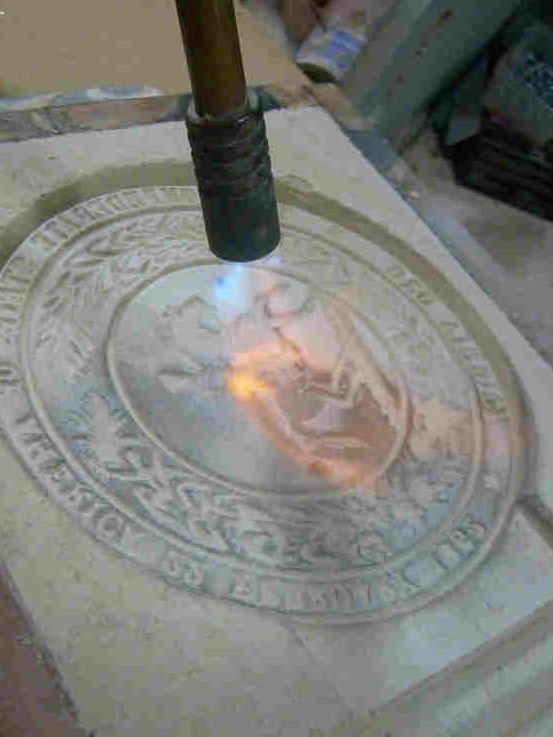
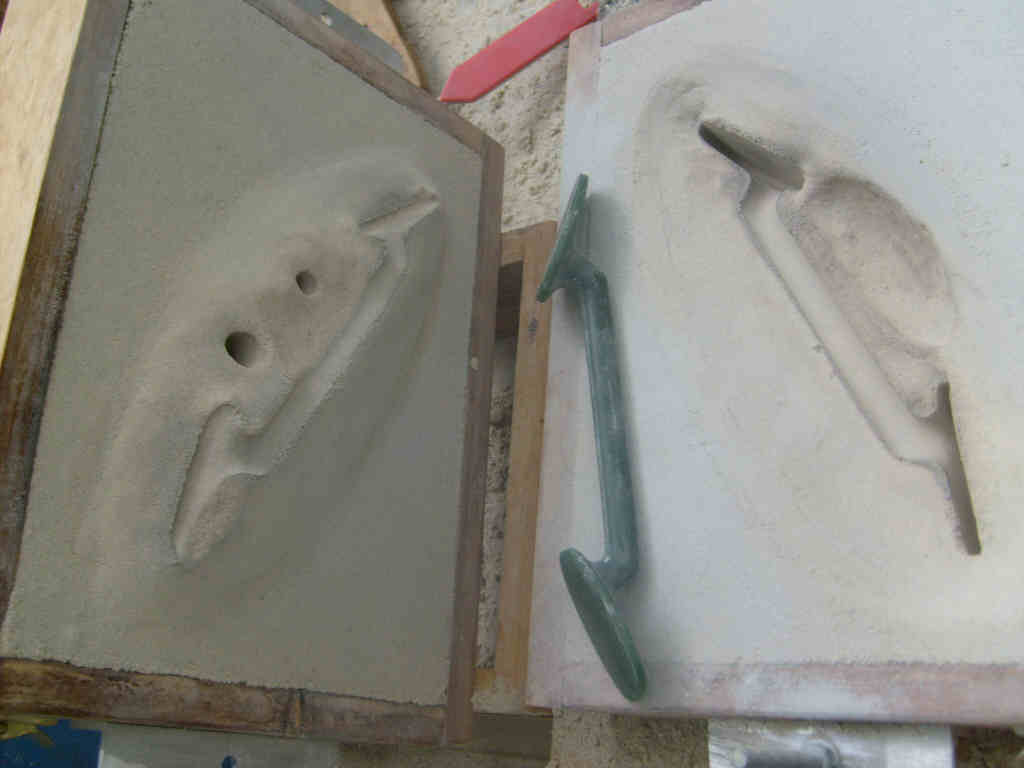
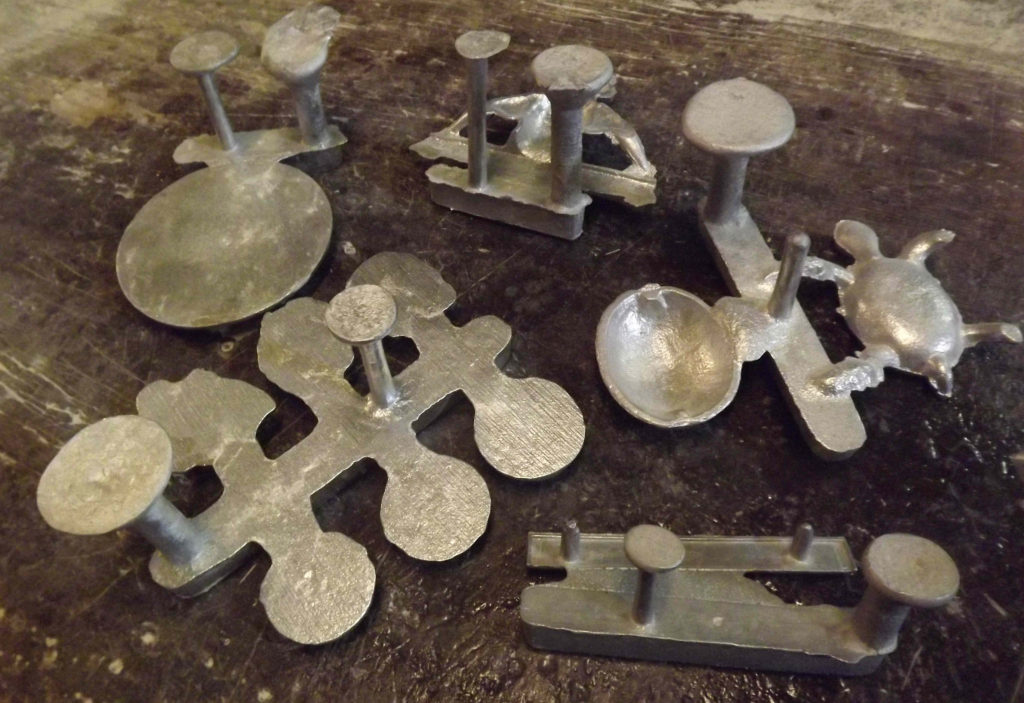
All castings have a gating system attached.
1. Metal is poured into the “sprue”.
2. Metal travels down the “runner”.
3. Sideways through the “gate” and into the casting.
4. There is a “pop-up” in the center of the runner, do not have the end of the runner.
The pop-up is 1/4″ and will release pressure once the mold is full.
Gating is removed after casting and re-melted.
Why do I need gating??
When you pour molten metal there is always dross, floating on top.
Dross is like the foam on beer, caused by exposure to the air and turbulence. During pouring, the dross goes to the end of the “runner” and sticks. Metal is skimmed as it travels through the gate, cleaning dross before entering the casting.